12月14-15日,“第六屆動力電池應用國際峰會(CBIS2021)”在江西贛州召開。來自國內整車、動力電池、材料、設備等產業鏈頭部企業和行業機構,以及國外部分在華產業鏈企業代表匯聚于此,共同圍繞新發展格局下,產業鏈交付、供應鏈安全與保障、雙碳目標與全球化市場新格局、材料技術突破與產業化應用等產業鏈核心議題進行深入交流探討。
圖為深圳吉陽智能科技有限公司董事長陽如坤作主題演講
在12月15日舉行的“成本壓力下的鋰電技術創新”主題論壇上,深圳吉陽智能科技有限公司董事長陽如坤發表了題為“動力電池制造新時代”的主題演講。
行業機構預測,在碳中和戰略背景下,到2060年,整個儲能產業的年均增長率可以達到31%的規模;同時,在全球汽車加速電動化的大背景下,動力電池的需求也將在未來數十年維持較高增速。
陽如坤指出,在這種產業大增長發展背景下,電池已經成為“通用目的產品”,是繼鋼鐵、CPU、機器人等產品后對人類社會最為重要的產品,已成為諸多產業的“心臟”,“作為關鍵性產品,電池制造不應該按照過去3C的方式,應該按照制造業發展的規律來管控電池的制造。
據陽如坤介紹,鋰電池產業經過二十多年發展也呈現了四大規律:
第一個規律是市場整個波動周期為五年,處于波動中前進,對電池產業尤其是裝備制造產業影響和挑戰都非常大;
第二個規律是能量密度和價格呈交叉發展的規律;
第三個是能量密度增長的規律,統計數據顯示電池能量密度大概10年翻一番,基于材料、電池結構和制造技術的創新,每年提升7%~8%左右;
第四個是電池成本下降的規律,從1991年索尼開始推動電池產業化,到現在下降了97%。機構統計發現,過去多年每年電池價格下降在18%左右,其中,隨著電池生產規模的擴大,成本下降更為明顯。陽如坤表示,未來數年,電池成本每年下降8%左右的水平應該可以維持。
陽如坤表示,過去10年,鋰電產業復合增長率維持在40%-50%,預計未來30年,復合增長率會維持在31%左右。
而上述規律之所以形成,一方面得益于電池材料和技術的不斷進步;另一方面國家政策規劃支持、碳達峰和碳中和等戰略的推行也起到很大作用。此外,電池制造技術、工藝日新月異,商業模式和消費習慣的不斷變化也促成了產業高速發展。
在陽如坤看來,盡管電池產業經過了多年的發展,但是過去電池制造完全是借鑒別的行業的經驗進行的簡單組合。
從電池制造的探索和理解來看,真正屬于電池自身產業的制造,從2020年,產業界才逐步意識和開始建立,“隨著產業進入純市場驅動階段,我們發現對電池制造基礎架構研究不多、標準體系未建立、電池制造工程體系未曾深度研究、電池材料和裝備深度結合較少,這些都是大規模擴產建設階段,整個產業遇到的挑戰。”陽如坤表示,電池制造應該回歸本源,從電池的材料制造、微米級甚至納米級極片制造,到電芯、模組、PACK的制造,都要探索出符合其自身產業特性的制造理念和標準體系。
陽如坤進一步解釋道,“整個電池制造應該從工程化角度來看電池的安全質量、規模、難點和痛點,要從本質上認識電池的機理,從微觀到宏觀的過程,電池制造標準化應是工程的實踐邏輯+驗證解決,這是我們思維的出發點或者工程化的出發點。”
陽如坤指出,當前,電池的制造安全恰恰是電池制造面臨的最大挑戰和問題,“過去人們談電池安全主要聚焦在材料和使用過程等方面,而忽視了制造本身。”
從電池制造安全來看,陽如坤認為主要是兩個層面:一是制造質量,包括整個工藝過程,必須實現PPM級的制造管控;另一個是電池制造標準體系的構建與落地。
陽如坤表示,目前汽車電池是“篩選”出來的,而不是直接造出來就能裝車的。目前全球最好的電芯制造合格率水平也就是95%~96%。未來能夠CPK2.0能做到以上,相信電池能夠不經過篩選就直接裝車或在儲能上使用,這是我們的愿景。
陽如坤認為,要實現上述愿景,需要實現電池制造的創新和突破,而這種創新和突破需要從工程原理出發?!?strong>目前電池制造最重要的在于標準建立,包括電芯的規格、工藝過程的標準化,這個過程需要進行數據定義、數據模型建立,最終才能實現智能化的數據分析。”陽如坤直言,如果主數據和標準都沒有定義清楚,整個電池要實現過程的優化是沒有太多的意義,很難實現真正統一的優化,同時過程閉環也是空中樓閣。
據陽如坤介紹,目前吉陽智能正在聯合企業、機構和政府將整個電池制造過程的數據進行定義,“用數據來管控整個電池制造過程的不確定性,能夠知道電池制造過程的切實性,這是我認為最重要的原則。”
陽如坤表示,目前電池制造的標準化痛點在于尺寸規格、制造過程和材料的標準化,主要內容還是在于電池材料類型、尺寸的數量及接口替換。電池尺寸規格的定義應是嚴格的定義,具備互換性,否則就沒有多大價值?!叭绻麄€工藝參數、測試標準、材料規格、制造過程,能夠實現很好定義,我認為能夠大大提升電池制造的合格率,同時也會使得電池成本通過標準化再降低20%-30%?!标柸缋ぱa充道,尺寸規格和標準不僅會影響材料的供給和采購的成本,還會影響制造成本及設備的優化和制造數據的收集,更重要的是會影響到智能制造數據模型的建立和優化體系的建立。
在標準體系方面,陽如坤建議應采用“前標準”的方法,也即先定義標準由整個產業來做,在推行的過程中不斷優化、完善,“從電池的產品、尺寸規格、制造規范、智能制造模型的定義均應采取這種‘前標準’的思路來解決,而不是放任標準野蠻生長,誰是行業老大,誰就成為行業標準的這種‘后標準’模式?!?/p>
未來,動力電池大規模制造會對精度、制造安全、成本和效率有著極高的要求,而通過標準化解決多尺度、多物理場耦合、多元、異構、海量數據、控形等問題,對智能制造的成本將會有大幅提升。
陽如坤指出,過去裝備的制造基本上還處于基于碼盤計數位置閉環階段;隨后迭代到邊緣計算。在邊緣計算層面,主要將來料的參數、過程參數、輸出參數拿到一個閉環過程實現制造的過程。我們并不清楚,如果我們能在第三個環,也就是制造產品的整個過程和來料、過程和制造質量實行閉環建立起來;例如張力,我們就能夠知道張力真正應該控制到什么程度,對電池的一致性和安全才是最好的,這是我認為整個產業的基本思想。
“基于這些,就可以把極片制造、電芯制造和PACK制造,和整個大數據實現閉環,當然這里最重要的還是數據定義,建立數據模型,最后實現制造過程的閉環?!标柸缋け硎?,“電池制造就是六大指標,把這六大指標進行很好的管控,未來整個電池能夠實現高質量發展,進而實現電池不再需要篩選,就能直接裝在汽車上?!?/p>

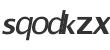